Article: Sustainability inside the blacksmith shop
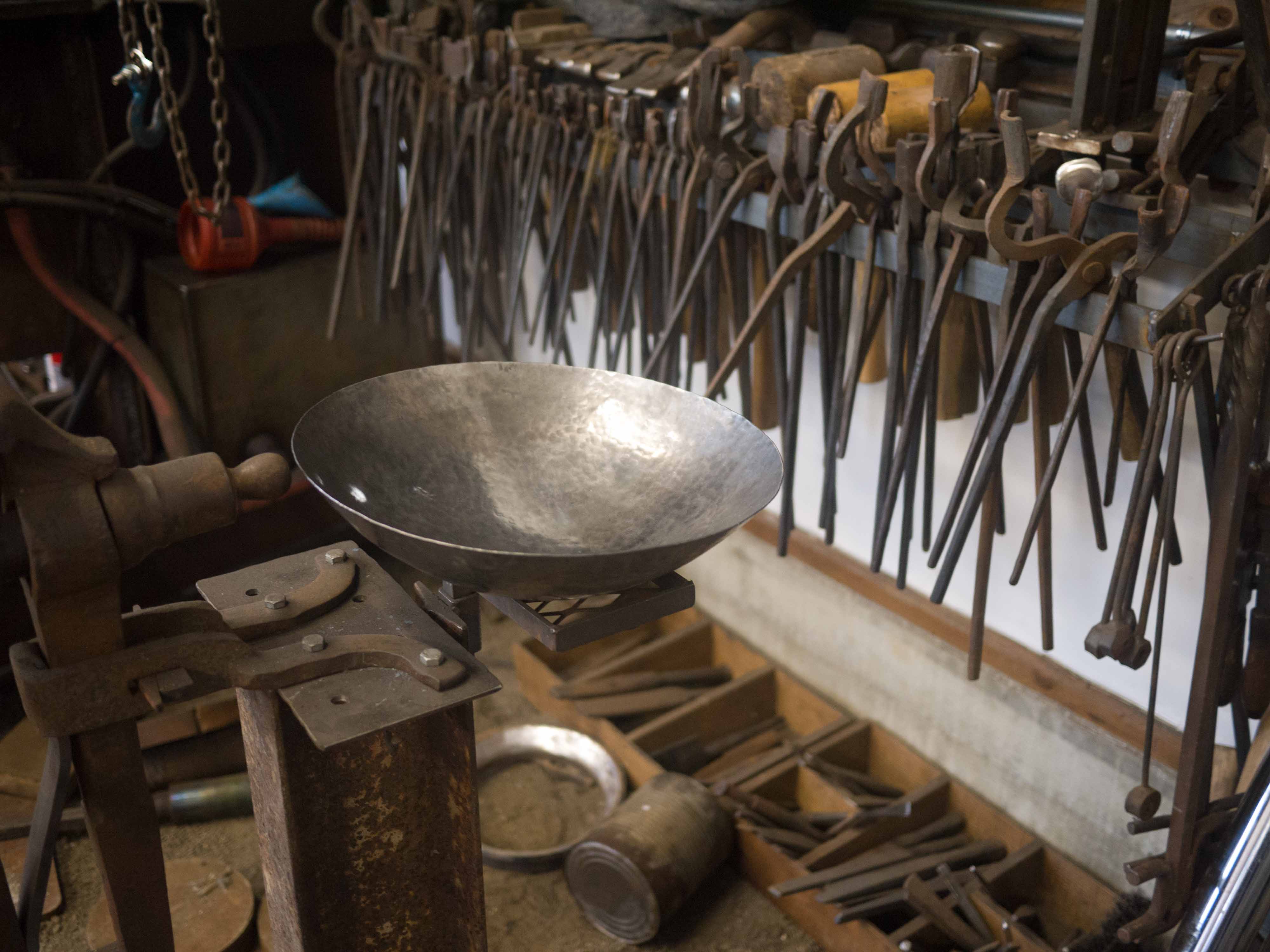
Sustainability inside the blacksmith shop
We are blacksmiths. Modern blacksmiths.
Blacksmithing went out of fashion during the industrial revolution because the blacksmiths birthed the machinery that launched the industrial revolution. So, why are there still blacksmiths today? Because there’s nothing that beats the look and longevity of hand forged metal. In addition,nothing can replace the flexibility in production of making products by hand. Any day, Erik can decide to make an entirely new creation, without re-tooling an entire factory.
Production of Steel and why ‘Made in the USA’ matters
All blacksmiths use steel to make hand forged iron work. Producing steel is an intensive process using huge amounts of energy. It is the highest CO2 emitting industrial activity in the world, generating close to 5% of the world’s total greenhouse gas emissions (Chandler, 2013). Global steel production also requires large inputs of coke (a sort of coal). Wastewater from the coking process is highly toxic, creating a soup of carcinogens, cyanide, and more.
According to the US Dept. of Energy, the US uses almost 100% recycled steel from scrap metal. And today, more than 70% of all steel production in the US uses electric furnaces (instead of coal/coke) to melt and reform steel (American Iron and Steel Institute, 2023).
More than 90% of the steel Newquist Forge uses in our products is manufactured in the US.
Production inside the shop is where the magic happens.
- Industrial steel production produces bar, plate, rod, tubes and other shapes of steel.
- The blacksmith shapes and forms it.
- Heat and/or hammering is very helpful in shaping steel.
Everyone is familiar with the glowing forge of a blacksmith’s shop. That glowing forge needs an energy source. The energy sources of choice for blacksmiths the world round is either coal, charcoal, or propane, with propane being the preferred fuel in the USA since it burns cleanly and is relatively cheap.
What sets Newquist Forge apart is owner and blacksmith. Erik has always been curious about sustainable fuels. It started 20 years ago when Erik devised an entirely new forge that was fueled by waste vegetable oil (things like vegetable oil used to fry falafels or donuts). He used a nozzle to create a fine enough mist to allow the oil to combust. It was a success, and for several years, he produced gorgeous architectural ironwork with the help of leftover french fry oil.
Induction Forge
Tired of smelling like french fries, Erik transitioned to an induction forge for more than 50% of our production. Induction uses electro-magnetism. An alternating electric current can create a magnetic field which produces heat in steel and iron which equals a very hot piece of metal ready to work under a blacksmith’s hammer.
Metal is heated in a forge, which looks like a miniature cave with a narrow mouth, and removed when hot to be worked on the anvil (the iconic hunk of metal that the blacksmith places hot metal on to hammer it into different shapes). Meanwhile, the propane forge is burning, consuming fuel. The induction forge, on the other hand, is only drawing electricity when there is steel being heated, otherwise it is in a standby mode.
Erik shapes copper tubes that allow various sizes of steel to go inside, or right up against. Copper heats quickly with the power of induction. It’s amazing to watch a cold piece of metal go from cold to white hot within 45 seconds. A propane forge takes several minutes to heat the same piece of steel.
The induction forge for us is also the perfect method because our electricity is produced with hydro-electric dams. Still, producing electricity isn’t perfect. The dams are on the Columbia river, which has seen a massive decline in wild salmon populations since the development of over 60 dams along the watershed of the Columbia river. Dams cause numerous problems to fish, including being a physical barrier for migrating fish to get through, heating the water to unsafe temperatures, chopping up fish in massive turbines…the list goes on.
The best answer is to use less, buy less, do less as a society and as individuals. When less electricity is needed, decisions can be made by policy makers to remove sections of dams where they contribute to declining salmon populations. That is one reason why we make products that have a lifetime guarantee, so that our customers only need to make a purchase once.
So why do we use a propane forge for some of the production?
Unfortunately, we can’t use our induction forge for everything! We would need 3 phase power (industrial) which we do not have at our quaint little blacksmith shop on the hill. In the meantime, Erik built 3 sizes of propane forges, mini, medium and large so that he uses only the exact size he needs, nothing more, nothing less. This is the kind of care we take with resources, always using the least amount of energy possible to create our products. We are currently experimenting using induction for seasoning our woks and pans to further cut down our footprint.
A complete decarbonization of our blacksmithing shop isn’t possible, yet, which leads us to find other ways to minimize or reverse our impacts, including creating quality over quantity, offsetting carbon emissions, donating and volunteering with local organizations that are protecting and rehabilitating salmon bearing watersheds.
The Northwest Watershed institute in our region has been working on an amazing project for over 20 years. I am thrilled by they focus on ONE watershed in our area, the Tarboo watershed which includes Tarboo Creek and the Tarboo-Dabob Bay, one of the few remaining intact lowland stream and estuary systems in Puget Sound (the region where our blacksmith shop is located).
They are attempting to restore the entirety of the watershed from tip to tail by partnering with 46 organizations, private landowners, and working with Dept of Natural Resources to protect and restore forest and waterways.
For example, they worked on a section of Tarboo creek that had been ‘channelized’. It was straightened out from its natural meanderings so that it wouldn’t flood farmland. But the farms are long gone, and the swift moving channels were making it impossible for salmon to come upstream and lay their eggs. Using excavators and lots of volunteers, they created a new creek bed with twists and turns, and planted trees along its length. Today, salmon can lay their eggs by the thousands in the gentle, gravel riffles of the creek, in waters kept cool by the shade of young trees.
You can check out their work at http://www.nwwatershed.org/
Works Cited
Chandler, D (2013, May 8) One order of Steel; Hold the Greenhouse Gas. MIT News. https://news.mit.edu/2013/steel-without-greenhouse-gas-emissions-0508
American Iron and Steel Institute (2023). Steel Production. https://www.steel.org/steel-technology/steel-production/